-
Our Location
Downtown Houston TX, Suites 88329
-
Online Support
API in Service Equipment
API inspection
Our wealth of knowledge gained from years of experience performing inspections on pressure equipment, pressure piping systems, and above ground storage tanks, combined with our extensive knowledge and experience performing NDE inspections on both in-service pressure equipment and new construction vessels in fabrication shops has allowed ZENGARY Inspection to become recognized as the industry leader in performing API visual inspections and repair and alteration oversight on in-service pressure equipment..
Our team includes multiple API inspectors who have years of documented training and experience in pressure vessel (API 510), tank (API 653), and piping inspection (API 570), cross-qualified and CGSB and PCN certified in multiple NDT disciplines.
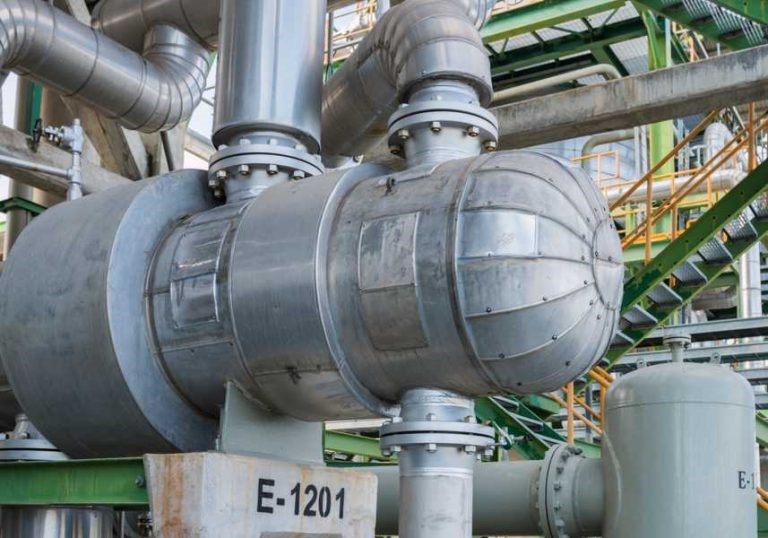
Inspection Services
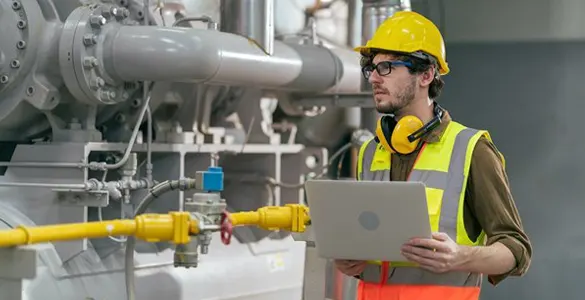
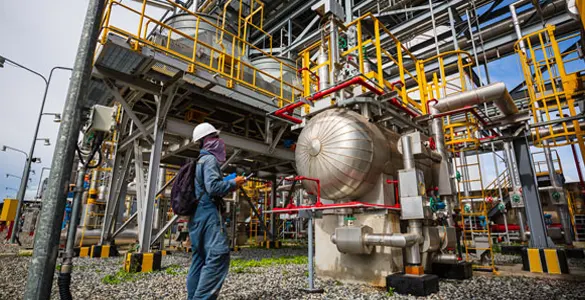
Installation inspections
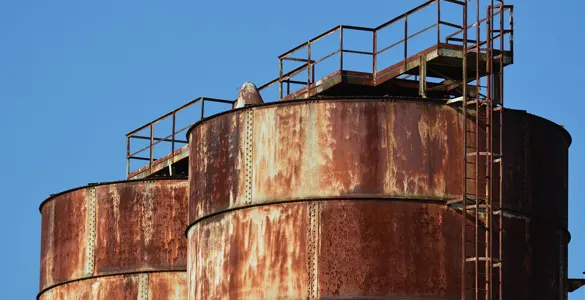
Atmospheric Storage Tank (API 653)
Our API Inspection services
-
Full service API inspections include
- Asset location and inventory verification of pressure equipment
- Internal Inspections of all types of pressure vessels
- External Inspections of all types of pressure vessels including PSV verification
- Installation inspections of pressure equipment
- Full inspection of above ground storage tanks, including detection and mapping of soil side corrosion below tank floors
- Inspection of pressure piping systems
- Oversight of repairs and alterations to pressure equipment and storage tanks (including performing required NDE)
-
Pipeline Integrity Inspection, (API 570 Pressure Piping)
Pipeline integrity inspections are one of the ways used to confirm the integrity of a pipeline, or confirm the accuracy of an MFL tools results. Our years of experience performing pipeline integrity inspections give us an advantage in knowing what to look for and how to find it. A typical pipeline Integrity Inspection will look for and contain the following:
- Documentation of the “as-found” pipe condition
- Inspection of coating and documentation of defects
- Documentation of external corrosion and pitting
- Profiling of external and internal corrosion for RStreng pipeline defect assessment
- Wet MPI (fluorescent or visible) of welds and corrosion areas for SCC
- Manual UT and automated UT mapping of internal corrosion
- Internal pit detection/sizing/profiling
- Dent deflection measurements
- Gouge characterization, measurement, and profiling
- Documentation of dig site conditions including soil condition, water, elevation,
- Bacteria sampling
- Soil samples collection
- Scale samples collection
- Testing for iron sulfate
- Arc strike removal
- Oversight of weld repairs or coating repairs
- Pipe-to-soil potential measurements